close
optimize
Optimization of Logistics Processes through Picking Strategies
3 August, 2023
edited on: 3 August, 2023
Optimizing warehouse processes is undoubtedly the key to cost savings and improved efficiency that logistics experts work towards. One of the crucial processes is “picking,” which allows for increased efficiency and quality of picked goods.
Below are several types of picking:
1. Order picking - Order picking is a key process in warehouse logistics that enables precise and efficient fulfillment of customer orders. This leads to increased customer satisfaction and a positive brand image, contributing to the enhancement of the company’s operational efficiency.
2. Batch picking - Batch picking allows for simultaneous picking of products for multiple orders, reducing the number of worker trips in the warehouse and minimizing the time required for picking. This results in more efficient utilization of human resources and increased process efficiency.
3. Zone picking - Zone picking facilitates better warehouse organization by assigning workers to specific zones. This increases transparency and control over the picking process while reducing the risk of errors. Workers become specialists in their designated zones, enhancing their efficiency and expertise in the specific area.
4. Wave picking - Wave picking optimizes work time and resources by utilizing specific time periods for picking. This enables better prioritization and reduces order fulfillment delays. Wave picking also helps in reducing congestion in the warehouse and improving product flow.
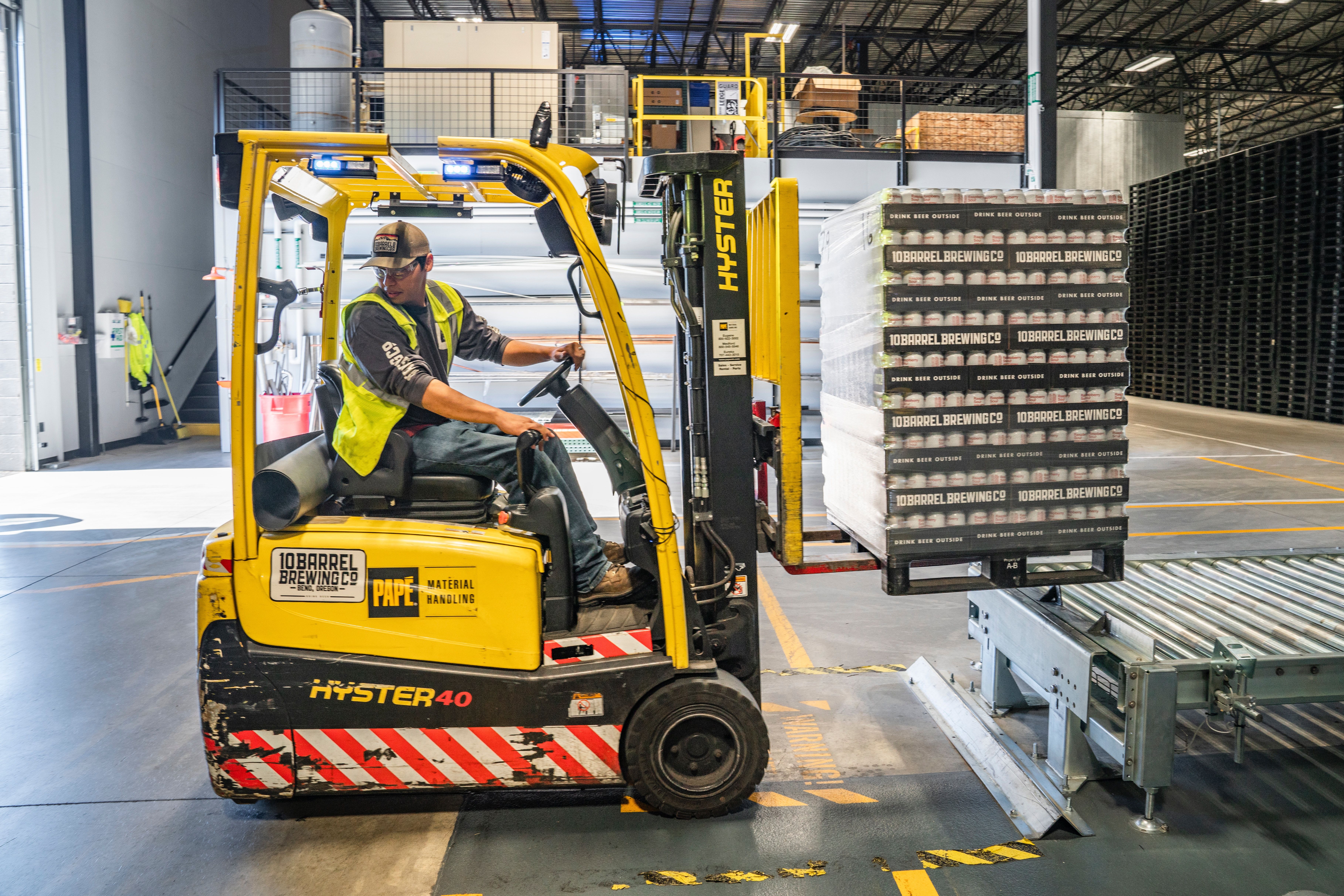
5. Pick and pack - Pick and pack combines order picking with immediate packaging, eliminating extra steps and operations. This leads to time savings and minimizes the risk of errors during the packaging process. The combination enables faster order fulfillment and prompt shipment to customers.
6. Pick to light - Pick to light is an advanced system that assists workers during the picking process. Workers receive clear instructions through illuminated cues, indicating which products to pick and how many. This enhances precision and speed in picking, minimizing errors, and optimizing the process.
7. Voice picking - Voice picking allows workers to pick products hands-free, providing instructions through voice recognition technology. Workers no longer need to refer to screens or paper lists, which increases ergonomics and reduces the risk of errors.
8. RF picking (Radio Frequency picking) - RF picking enables real-time information flow about the warehouse’s status and picking through radio frequency technology. This allows for on-the-spot resource management, priority adjustments, and minimizes errors caused by outdated data. The RF picking system significantly accelerates the picking process and enhances its accuracy.
9. Pick-by-robot - Pick-by-robot involves using robots to automate the picking process, significantly increasing productivity and precision. Robots can work continuously, offering 24/7 picking capabilities, which is particularly beneficial for handling large order volumes.
10. Pick-to-cart - Pick-to-cart allows workers to efficiently gather products and place them directly onto a picking cart. This minimizes unnecessary movements in the warehouse, saving time, and increasing overall efficiency.
6. Pick to light - Pick to light is an advanced system that assists workers during the picking process. Workers receive clear instructions through illuminated cues, indicating which products to pick and how many. This enhances precision and speed in picking, minimizing errors, and optimizing the process.
7. Voice picking - Voice picking allows workers to pick products hands-free, providing instructions through voice recognition technology. Workers no longer need to refer to screens or paper lists, which increases ergonomics and reduces the risk of errors.
8. RF picking (Radio Frequency picking) - RF picking enables real-time information flow about the warehouse’s status and picking through radio frequency technology. This allows for on-the-spot resource management, priority adjustments, and minimizes errors caused by outdated data. The RF picking system significantly accelerates the picking process and enhances its accuracy.
9. Pick-by-robot - Pick-by-robot involves using robots to automate the picking process, significantly increasing productivity and precision. Robots can work continuously, offering 24/7 picking capabilities, which is particularly beneficial for handling large order volumes.
10. Pick-to-cart - Pick-to-cart allows workers to efficiently gather products and place them directly onto a picking cart. This minimizes unnecessary movements in the warehouse, saving time, and increasing overall efficiency.
With a comprehensive understanding of these picking strategies, businesses can optimize their logistics operations, achieve cost-effectiveness, and provide exceptional service to their customers.
reading time
4minute
contact
Address
Meritus S. A., based in Warsaw,,
ul. Prosta 70, 00-838, Warsaw
NIP: 5273148508
REGON: 540723424
KRS: 0001151166
Equity in the amount of 100,000 PLN
E: office@pinquark.comul. Prosta 70, 00-838, Warsaw
NIP: 5273148508
REGON: 540723424
KRS: 0001151166
Equity in the amount of 100,000 PLN
follow us
contact us
Get in touch
We care about your feddback. Please contact us when you need.